through a series of rigorous quality control steps from raw material inspection to finished product testing, kaibo can guarantee the quality and reliability of reducers, meeting the demanding requirements of diverse industrial applications and contributing to the overall success of mechanical systems.
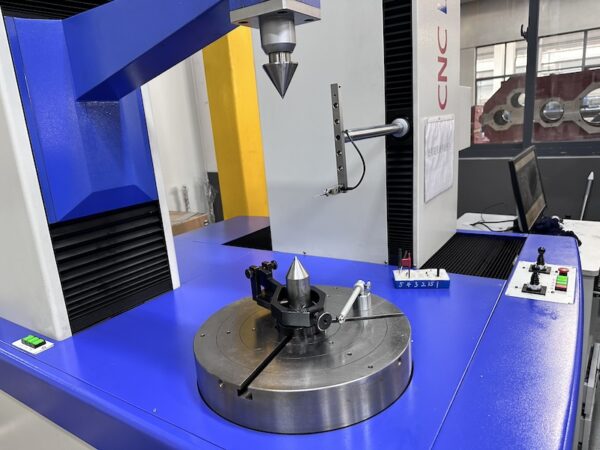
In the manufacturing of reducers, strict quality control is of paramount importance to ensure the reliable performance and long service life of these crucial mechanical components. The following steps and measures are typically implemented throughout the production process.
1.Raw Material Inspection: High-quality raw materials are the foundation of excellent reducer products. Before entering the production line, all incoming materials, such as gears, shafts, housings, and bearings, undergo meticulous inspection. Advanced testing equipment is used to check the hardness, dimensional accuracy, and material composition to ensure they meet the specified standards. For example, spectrometers can analyze the chemical elements in metal materials precisely, and coordinate measuring machines (CMMs) can measure the dimensions of components with extremely high accuracy. Any substandard materials are immediately rejected to prevent potential quality issues from the very beginning.
2.Machining Process Monitoring: During the machining of reducer parts, continuous monitoring is essential. CNC machines equipped with sensors constantly track parameters like cutting forces, tool wear, and machining temperatures. If the cutting force exceeds the normal range, it may indicate problems with the tool or machining process, which could lead to dimensional inaccuracies in the parts. By closely observing these parameters, operators can make timely adjustments, such as replacing worn tools or adjusting cutting speeds, to ensure the precision and quality of each machined part.
3.Assembly Quality Control: The assembly stage is critical as it directly affects the overall performance of the reducer. Workers follow strict assembly procedures and use specialized tools to ensure proper installation of all components. Torque wrenches are employed to tighten bolts to the exact specified torque values, preventing over-tightening or under-tightening that could lead to component damage or loosening during operation. Additionally, before final assembly, each part is cleaned thoroughly to remove any debris or contaminants that could interfere with the smooth operation of the reducer.
4.Finished Product Testing:Once the reducer is fully assembled, a comprehensive suite of tests is carried out. Performance tests measure parameters like speed reduction ratio, torque output, and efficiency under various load conditions. Vibration and noise tests are also performed to evaluate the smoothness of operation. Excessive vibration or noise could signify problems such as unbalanced components or improper meshing of gears. Only those reducers that pass all these tests with flying colors are deemed qualified for shipment, ensuring that customers receive products of the highest quality.
In conclusion, through a series of rigorous quality control steps from raw material inspection to finished product testing, kaibo can guarantee the quality and reliability of reducers, meeting the demanding requirements of diverse industrial applications and contributing to the overall success of mechanical systems.